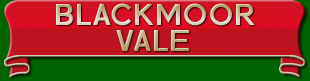
VALVE GEAR
Bulleid like other engineers had long felt that it was not ideal to have working parts exposed to the elements where they were subject to all the grit and muck thrown up from the track. He also thought that steam engines should get nearer to the internal combustion engine which enclosed the working parts and used pump lubrication to keep it all running smoothly. Another advantage of enclosing the valve gear would be the reduced day-to-day maintenance.
What he came up with was a modified gear contained, with the inside big end, in an oil bath between the frames driven by chains from the middle-driving axle. It was called an oil bath but the depth of the oil was only 2 inches. Reversible pumps situated at the bottom of the sump distributed filtered oil by means of pipes to the moving parts.
The final drive to the piston valves was by means of a rocker, which operated the beam between the valve heads. Because of this Bulleid decided to use outside admission as this avoided the use of high-pressure glands.
Bulleid's valve gear was very free running when well maintained. The valve events stayed the same for all cylinders when wear developed. Bulleid didn't mind valves over running slightly as long as it wasn't on just one cylinder especially after his experiences on the LNER where over-heated big ends on the middle engine were a constant problem.
The steam reverser shown above is the early version, use only on the first ten Merchant Navys, with the lever to the valve gear attached to the the rod between the two cylinders. Below shows the later version, used on the later Merchant Navys and the Light Pacifics, with the reverser mounted further back and the drive attached to an extended piston rod. As the rod passes straight into the oil bath it would seem easier to create a seal with this arrangement. The reverser used was a development of the Eastleigh and Ashford versions and included elements of both.
Unfortunately there were design errors in the casing used for the oil bath it being too rigid plus thick and thin sections were welded together without appropriate curves to allow flexing, causing cracks to develop. The seals to allow axle movement were inadequate plus the cover and breather sealing was poor. All this allowed water and grit to enter and the oil to leak out. These faults could probably been overcome but with post war conditions and then nationalisation there was never the will, time or money to do it.
Clicking on the diagrams above will bring up a larger resolution GIF in a new window.